When we moved into our Grade II listed house, one of the first things we noticed—especially in winter—was how much heat was escaping through the windows. It’s no surprise: up to 40% of a home’s heat can be lost this way. In most modern homes, the fix is straightforward—install double or even triple glazing. But for us, planning permission for sealed units was refused.
That left us with two choices: secondary glazing or finding ways to improve the original timber frames. And after much research, we decided to repair our original window frames, which seemed the most cost-effective and environmentally friendly option.
Glass Matters
Double glazing, especially sealed units with a low-emissivity (low-e) coating and inert gas between the panes, can make a huge difference in thermal performance. Triple glazing might seem better, but depending on your building and climate, the extra pane doesn’t always justify the cost or weight.
Sadly, most window glass isn’t recycled—even though it’s technically fully recyclable. In practice, it often ends up in landfill or rubble because it’s hard to separate and process. Plastic alternatives like acrylic or polycarbonate didn’t appeal to us either—they just don’t perform as well and have a higher environmental impact long-term.
Working with Original Timber Frames
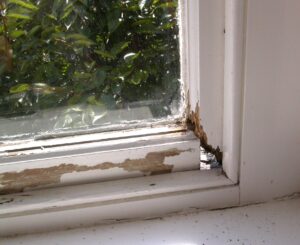
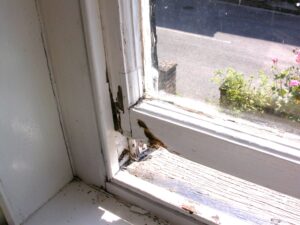
Since we couldn’t install modern sealed units, we decided to restore the existing wooden frames. That meant repairing rot, replacing failed putty, fitting new draught seals, and repainting. It was time-consuming but surprisingly satisfying. And unlike uPVC, wooden windows can actually be repaired rather than replaced.
Well-maintained hardwood frames can last over 50 years, and they have a negative carbon footprint. The only downside is they can warp over time, causing draughts—but careful maintenance helps a lot.
For extra insulation, we added lined curtains and The difference was immediate and noticeable.
What About Other Frame Materials?
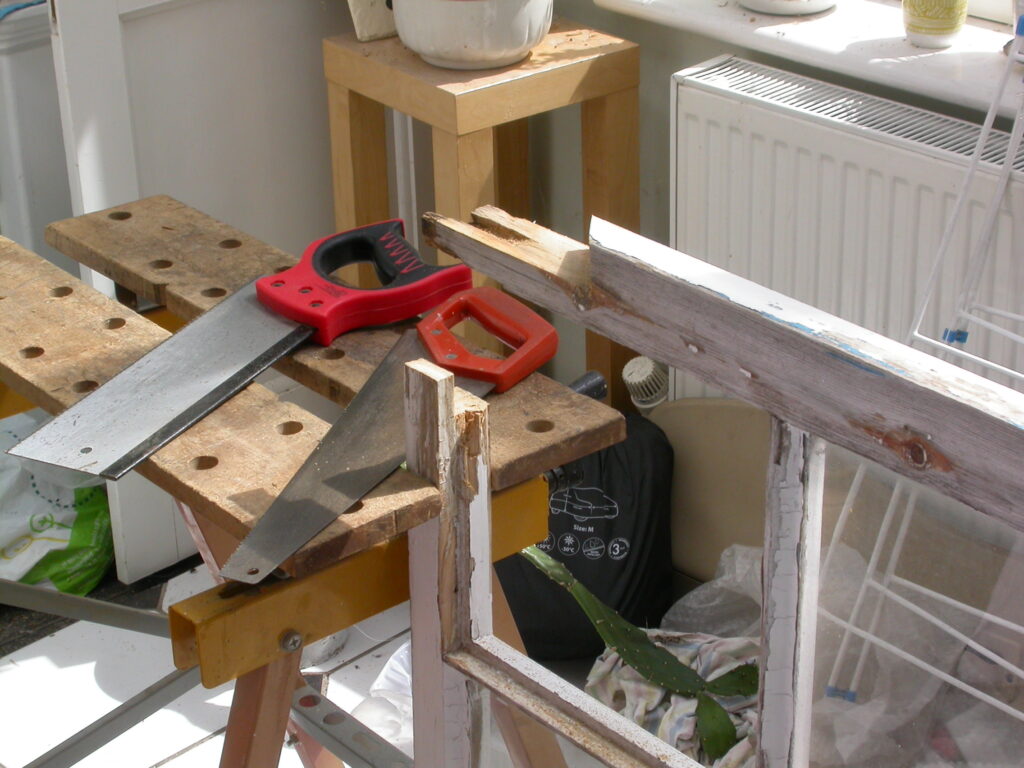
Through our research into the most efficient and sustainable way forward, we discovered that:
- Aluminium looks sleek and lasts around 45 years. It’s energy-intensive to produce, but usually made with renewable electricity and is almost always recycled (often 95% recycled content). However, it needs a thermal break to stop heat escaping—and in our case, it was a no-go for the planners.
- uPVC is cheap and common, but not very sustainable. Its production has a high carbon footprint, it only lasts around 30 years, and while it can be recycled multiple times, in practice only about 20% actually is.
- Steel or fibreglass were non-starters—rarely used, with no major benefits.
Final Thoughts
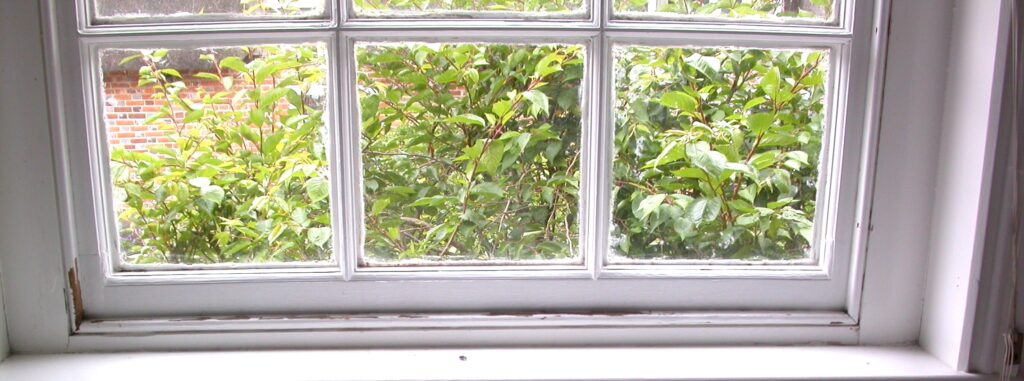
Living in a listed building means accepting some compromises—but it’s also a chance to get hands-on and make sustainable choices. Repairing our old wooden windows wasn’t just a workaround—it felt like the right thing to do, both for the house and the planet. And it turns out, with a bit of care and creativity, even a drafty historic home can be made cosy.


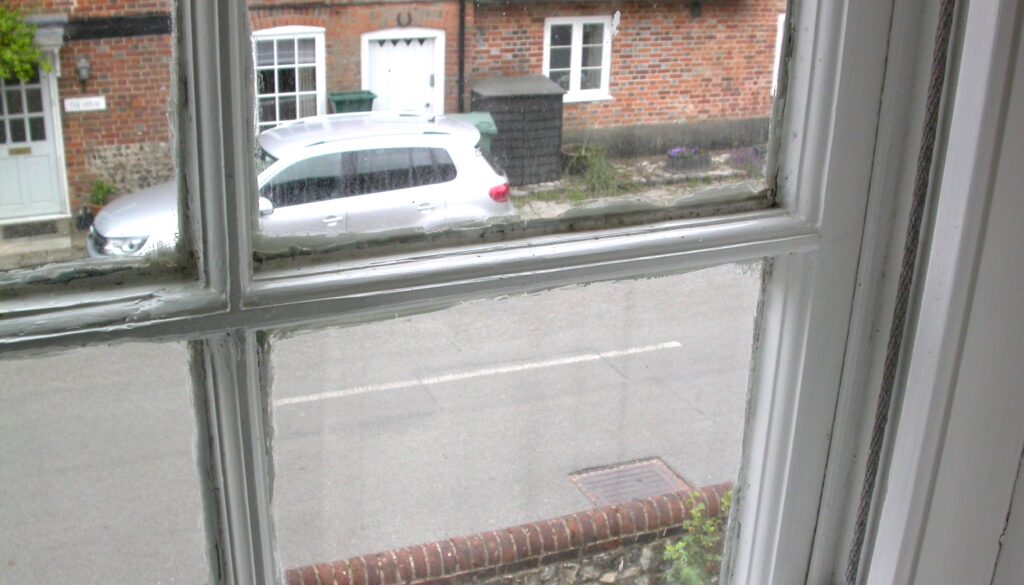